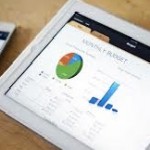
Norcott Technologies Invest in mobile technology
Norcott Invest in iPads.
To further enhance Norcott’s strict Quality Monitoring and Production Control system, a major investment has been made in developing bespoke solutions for the latest mobile technology and Bluetooth barcode scanners.
Software was developed in-house on the .NET platform creating a set of REST API services to enable database connectivity wirelessly to the iPads. Applications developed for the iPad using Apple’s XCODE and .NET WPF for windows are now in use by Norcott staff to record on every aspect of production for subsequent monitoring and analysis by Management.
The systems also integrate with production so that the real-time status of a job can be tracked. Integration into the company’s existing AOI system and GNC system provide operators with a wealth of information at their fingertips.
Ted Reilly, Senior Business Process Developer commented: “Having come from a Quality Management background in a manufacturing environment, I was keen to create a powerful system that would provide staff with all the information they need at their fingertips. The beauty of adopting mobile technology, especially on the iPad with BT scanners, is that it becomes completely portable and members of Quality staff can use the system at any time or place within the organisation.”
The system known as iOracle has a rich set of reports that can be used to analysis non-conformances down to a component pin level and underpinning this is a set of summary reports that calculate PPM, Sigma and Test Yields dynamically.
Norcott Develops Production Scheduling System
An Advanced Production Scheduling System has been developed in-house with the aim of gaining much accurate and tighter control over the scheduling of production batches. This was deemed essential as the Company increases productivity with the commissioning of a second SMT Assembly Line.
The system uses a very detailed timing/costing model that permits calculation of SMT placement times down to the component level and even recognises u-BGA and ultra fine QFP devices making compensations to ensure accuracy. An automatic refresh feature ensures the displayed schedule, which is provided in the SMT area via a large LED monitor, reflects almost instantly changes made by Norcott’s Operation Manager, Andrea Williams.
Another unique feature of the system is it’s integration with Norcott’s Quotation System. This permits Sales staff to issue automatic alerts to the Operations Manager of pending jobs so that capacity can be reserved. In addition to this as with iOracle above, when a job is loaded onto the schedule, its associated history is checked and Quality alerts pop-up to ensure awareness is raised.
To further assist control, the system has in-built resource monitors that display process loading and integration with the Production/Quality scanning systems provides real-time progress of any job.
Andrea Williams, Operations Manager commented: “Norcott used to control its production system manually using an EXCEL spread-sheet. The new system now allows me to plan in very close detail every aspect of a production batch and perform what-if scenarios when assessing availability. With AS9100 approval placing greater emphasis on the monitoring of KPI’s like On-time Deliveries, early signs would indicate the system is helping to improve SMT systems uptime OEE figures by better process loading.”